Mallion is the name of my hybrid violin design and the coinciding family of bowed instruments modeled after it.
My designs are made from the traditional materials of wood, and also steel.
They are a unique culmination and balance of beauty, technology, weaponry and, perhaps, sadism. To procure my place among violinmakers everywhere, I offer this brief history about myself.
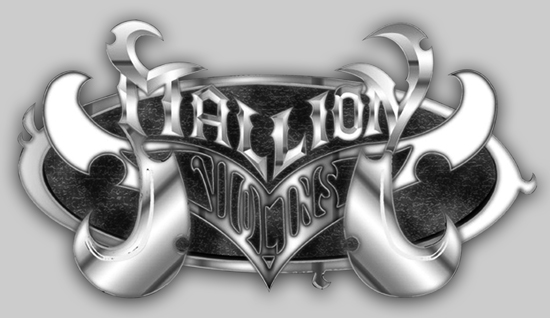
My first violin was a family heirloom that I inherited from my great-uncle’s father. It had sat in a closet for 83 years before it was given to me, and it was a beautiful time capsule of decades past. When pulled out of the closet, it had three rotted and broken cat-gut strings still attached to it. The bridge had been nearly shaved flat to facilitate easier chord movement and I found a rattlesnake tail sliding around inside of the body of the violin: an old superstition among fiddlers to make the instrument sound more beautiful.
From this inheritance, I developed a tremendous amount of love and respect for the Stradivarius tradition of the violin family, which the heirloom was modeled after. From that respect and love, I chose to create my own design.
The only part of playing the acoustic violin that I have never enjoyed is the fragility of the instrument; I have often felt it is like playing an egg with strings. In response to this drawback, I have created a kind of violin and violin family that are virtually indestructible compared to standard acoustic violins or even other electric violins.
The production and invention of the first Mallion was a necessary conglomerate of several of my skills. My life has been a scattered mess of various educations: I have attended Kansas City Art Institute, I have had apprenticeships with blacksmiths, pewterers, and jewelers, I have had lessons with some old school fiddle players and I have spent a few years at Missouri State University, graduating with a BFA in metal sculpture from Metropolitan State College of Denver.
In order to complete the first violin, I used everything I had ever learned about drafting, design, composition, metalwork, woodwork, music and stamina. It was my first piece of fully functional sculpture (besides furniture) and the first prototype was a year in production. While making the prototype, I worked in a blacksmith shop, my grandfather’s woodshed, and a college sculpture lab. During construction I, did and do, cut, forge, hammer, curse, weld, braze, glue, drill, tap, sand, grind, curse again, hammer again, braze again, grind again, stain, powder coat and solder in order to complete my mission.
Mendon, the contrabass, was the second instrument I created. The creation of its prototype was spread out during the course of a year and a half, and the construction process was very labor intensive. The sheer size of the instrument caused a lot of problems initially because of the fact that metal tends to bend under stress of heat and string pressure unless properly reinforced. I found that without a proper steel “spine” for reinforcement, the entire instrument would bend when tuned to the proper pitch. Also, the weight of the instrument made it necessary to devise a way for the instrument to stand on its own without any human effort.
The cello, Midian, involved more technology, including plasma cutting and CAD based programming. Like the bass that was built before it, Midian stands upright by itself to avoid any weight issues. Midian completes the major design challenges of the Mallion family of strings, promoting a gorgeous new hypostasis of visual and physical strength that parallels the power produced by the instruments musically.
I am now located in Japan, and I create instruments on a commission basis. My latest creation is the “Hung Mallion Scythe“ created for Lyris Hung of the New York heavy metal band “Hung”.
-Erich Meatleg –